Transformative Commercial Roofing Systems for Your Business
At Exceptional Roofing LLC, we offer more than just commercial roofing services. We provide peace of mind by protecting your property, business, and employees.
Reach Out Today
Who’s Protecting Your Property?
Are you confident your commercial property will stay dry when the rainy season arrives? The professionals at Exceptional Roofing LLC are here to provide peace of mind and protection with reliable commercial roofing solutions throughout Kentucky, Illinois, Indiana, Mississippi, Missouri, Tennessee, and Southern Ohio. We can inspect the condition of your business’s roof, provide an honest assessment, and make recommendations to prevent damage to your property. Our reliable process ensures your roof is prepared to handle the harshest weather conditions.
Learn More
A Roofing Solution for Every Problem
Your roof is the most critical feature of your facility. From UV rays to heavy rains and snow, it should be able to withstand whatever mother nature throws its way. However, over time, it can begin to deteriorate. Exceptional Roofing LLC has been providing high-quality roofing solutions for businesses throughout the areas we serve for over 20 years. Our experience and reliance on the best products on the market mean we’re able to tackle any roofing project of any size. Find the right commercial roofing service for you:
Communities We Serve
Speak to Us
A Legacy of Excellence

High-Quality Products for Every Project
At Exceptional Roofing LLC, we believe choosing suitable materials is the key to high-quality roofing systems. All our roofing projects are completed using proper techniques and superior products. As a Duro-Last® authorized contractor, you can feel confident about our commitment to craftsmanship.
Learn More
Discover What Makes Us the Preferred Roofer
It’s more than just a roof. It’s an investment in the continued success of your business. At Exceptional Roofing LLC, our team is committed to helping you protect your future with our exceptional roofing solutions. Throughout our decades of service, we have earned the reputation of being a reliable partner. We take the time to understand your needs and concerns and provide thoughtful solutions to address your problems. Learn why more businesses choose us for their roofing services:
- Over 20 Years of Experience
- Licensed and Insured
- Continual Communication
- High-Quality Products
- Se Habla Español
0+
Satisfied Customers
0+
Cities Served
0+
Years of Experience
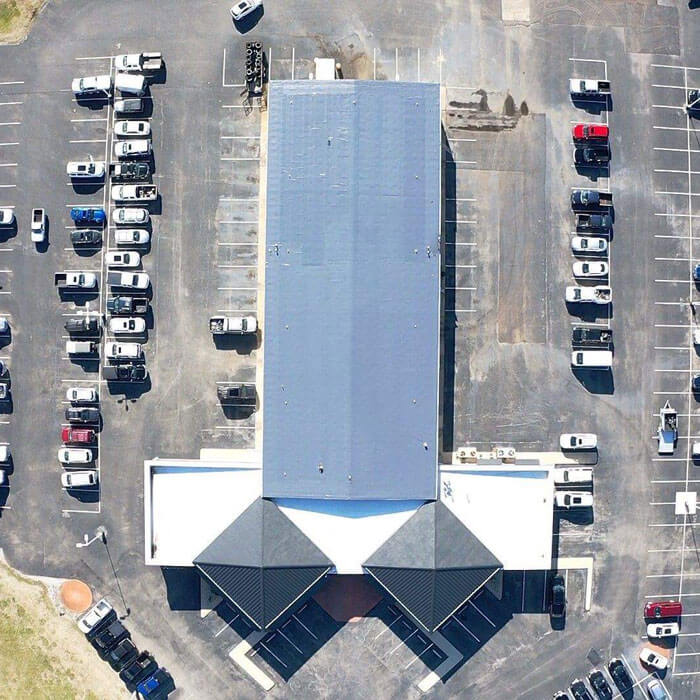
Invest in Your Commercial Property
When it comes to safeguarding your property, you can’t make a better investment than upgrading your roof. Whether you need ongoing maintenance, one-time repair, or a complete replacement service, choosing a reliable roofing company can help you save money on expensive water leaks and roof damage while enhancing the curb appeal of your business. If you notice any issues with your business’s roof, you can count on our team for an honest assessment and exceptional services.
Learn More
Your Reliable Roofing Contractor
A damaged roof can quickly lead to leaks, mold growth, and structural issues. Count on us to protect your property.